22nd Feb 2018
Why Foam Fenders are Replacing Pneumatic Tube Systems
Pneumatic tube systems and buoyancy aids have a common flaw when it comes to use within a marine environment. If a pneumatic (air) tube is damaged, suffers abrasion or is punctured, then the system will inevitably deflate or sink and no longer provide adequate protection.
Polyethylene (PE) is one of the most extensively produced plastics. Polyethylene foam is commonly used within a marine environment due to factors that make it an ideal material for floatation devices such as its resistance to fresh and saltwater, floatability, low mass, flexible structures and its durability against impact.
Polyethylene foam is made from recycled polymers and involves the melting of polymer compounds. The structure of polyethylene foam is comprised of small bubbles that are commonly referred to as “closed cells”. A wide range of shapes can be accomplished with closed cell polyethylene foams and it is most commonly produced in large sheets. However, it can be heated into solid foam cores which produces a thermal bond between foam layers. This construction creates incredibly durable foam for the abrasive of marine environments.
Foam filled fenders are reported to absorb 40% more energy than pneumatic fenders.
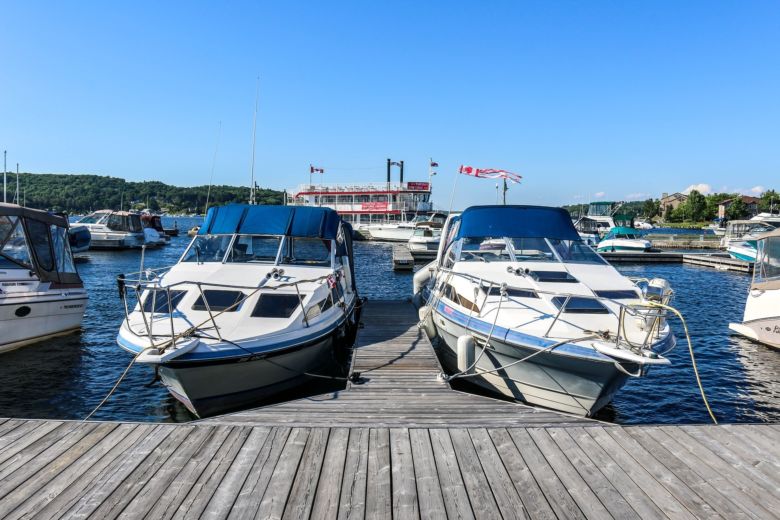
What are the benefits of using closed cell polyethylene foam?
Absorb impact
Each closed cell is completely enclosed and as they are packed tightly together, they will not compress or settle over time. That means polyethylene foam can absorb impacts without damage, and won’t crush or flatten at point of contact when berthing. They have low corresponding reaction force and unlike pneumatic tube systems which will lose shape and buoyancy with heavy impact.
The rebound effect that can be caused with pneumatic systems is greatly reduced by a foam fenders absorbing energy.
Unsinkable
Due to the separate closed cell structure, PE foam won’t allow water to migrate into the foam as each cell is enclosed. Polyethylene foam doesn’t act like a sponge and will not absorb water, even when the skin is punctured the foam fenders will not sink like pneumatic fenders. Even if the abrasion occurs against the skin of a foam fender, the fender will still maintain shape and continue to float.
Won’t mark a ship’s hull
Foam fenders provide protection to the vessel, as well as the protection to the floatation core concealed within the foam during deployment and recovery. They can be installed fixed or floating, and their skins will not mark a ship exterior.
Durable against wear and tear
Due to their closed cell structure, foam fenders are incredibly durable when faced with the daily marine environment and they are exceptionally resilient to punctures.
Low maintenance
Polyethylene foam fenders require little maintenance as they don’t have inflation valves to maintain, there is no pressure relief required and they’re easily repaired.
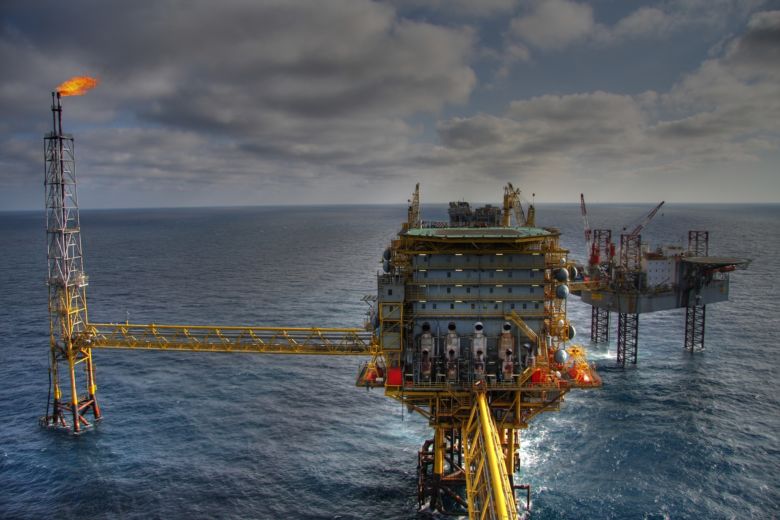
Polyethylene foam fenders usage
PE Foam fenders are most commonly used for:
- Safety boats
- Safety boats on large vessels
- Oil rigs
- Dive boats
- Ship to ship and ship to dock applications
- Docks, wharves and piers
Foam fenders are commonplace in boats that face more physical day-to-day contact and require better durability to withstand their environment. Many large vessels use foam fenders in onboard inflatable boats due to metal platforms and structures, as foam fenders are resilient to punctures, where as pneumatic air systems are easily ruptured and can become flat.
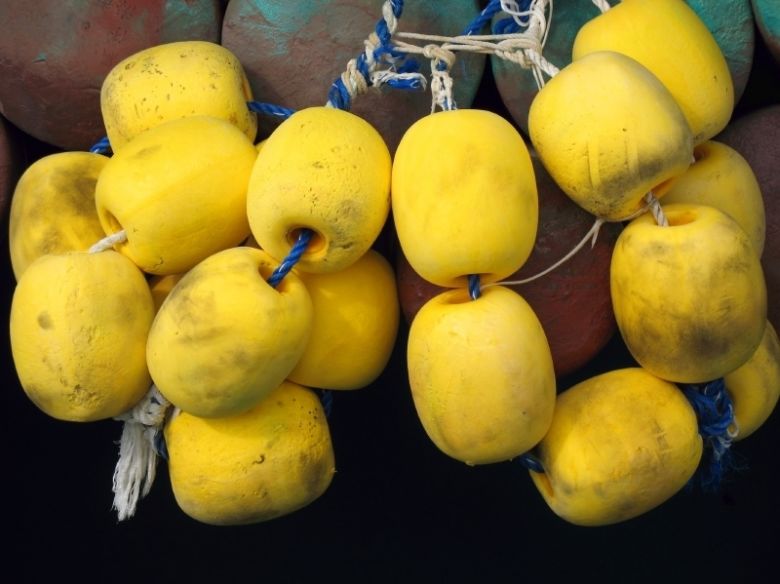
At Zouch, our specialist marine and flotation foams are strong, durable and lightweight, they’re algae and fungus resistant, with low water absorption – ideal for a whole range of buoyancy, flotation and protection products. Our in-house design and development engineers are constantly focused on optimum comfort and cost effectiveness, as well as on reducing environmental impact and vehicle weight.
For even more peace of mind, many of our materials carry the SOLAS approval – the international maritime standard for Safety of Life at Sea in construction, equipment and Operation.
Get in touch with our expert team to discuss your specific application and we will support you from prototype to road-ready product.