15th Feb 2018
The Benefits of Using Polyurethane Foam in the Automotive Industry
Polyurethane (PU) is a polymer that is widely used throughout the automotive industry for vehicle manufacturing. Most polyurethanes are thermosetting polymers and that means they do not melt when heated. The most common uses of polyurethane in the automotive industry are in the manufacture of high-resilience foam seating, rigid foam insulation panels, B-pillars, headliners, suspension insulators, bumpers and other interior parts of a car.
In the UK in 2016, there were 1.7million passenger cars built which was an increase of 8.5% and it was the highest output for 17 years. Due to passenger cars becoming a rapidly growing market, the benefits of using polyurethane foams within the sector are extensive and vehicle manufacturers are becoming even more receptive to its advantages. Emissions, the environment, safety and affordability are just a few of the factors which automotive professionals must consider when embarking on new vehicle design and engineering.
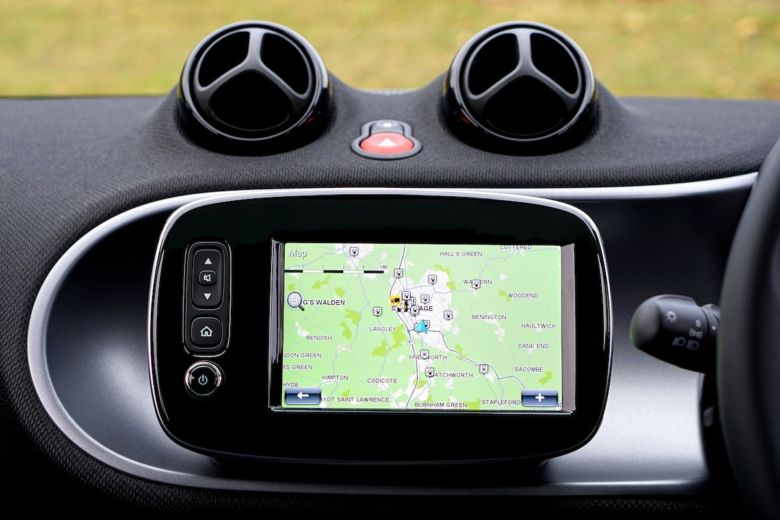
Reduces noise
Whilst in previous years, car manufacturers mainly focused on keeping the sound of outside road noise out, due to the evolution of technology and motorist’s requirements for in-car wireless systems, such as GPS and handsfree communication, the interior acoustic design of a vehicle has become considerably more prevalent. The prime areas for in-car noise originate in the tires, engine and suspension. PU is widely used because of its ability to insulate and reduce interior sounds by absorbing noise and vibrations by injecting PU into the body cavities.
Not only is noise reduction essential for comfort but also fundamental when it comes to safety. Loss of concentration has a negative impact on driving behaviour and causes longer reaction times, inadequate observation and hazardous braking.
Lightweight
Vehicles are synonymous with fuel consumption and as a result of the lightweight qualities of PU, it drastically reduces vehicle weight and thus, critically improves vehicle emissions. Whilst steel is likely to remain the primary material of vehicle structures, as well other high-strength steel grades, materials such as polyurethane are aiding the need and requirement for significantly reducing weight safely. PU is also being used in electric vehicles where metal was traditionally used in design, it’s now being seen in exterior cladding, roofs and hoods, as a safe, lightweight solution.
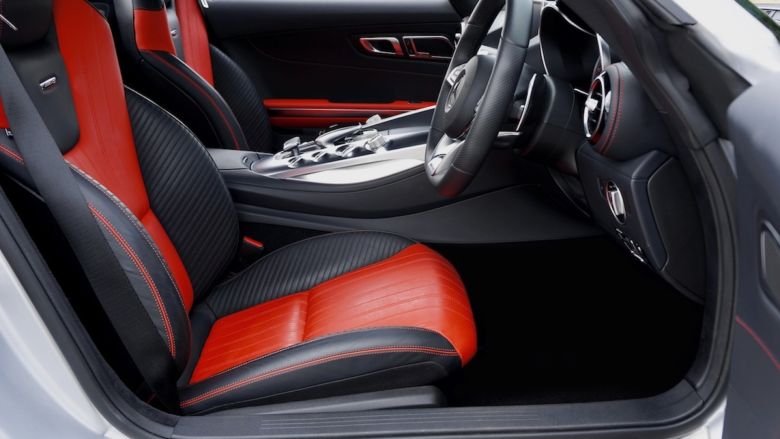
Versatile for design
Polyurethane is versatile and can easily be adapted for freedom of design, as well as being greatly affordable. PU is often used in vehicle seating due to its superior comfort and because of its reduced material intensity, it is greatly durable. Traditional metal reinforcements used on a vehicle bodies are more often replaced by foam because of ease of adjustment based on design changes. Its high resistance to heat and its structural stability allows it to be moulded and tailored dependant on the required customisation.
Recyclable
As well as being used to reduce emissions, PU has become more popular due to its recyclability. It’s important to businesses and consumers alike that more recyclable materials are used to reduce the overall environmental footprint.
Durable
The finish of a vehicle needs to be desirable to a consumer but also durable due to the wear that it experiences daily. Vehicles require protection against numerous environmental effects such as temperature, chipping and dents caused by accidents. PU increases crash performance and stiffness levels, whilst continuing to reduce the overall weight of the vehicle.
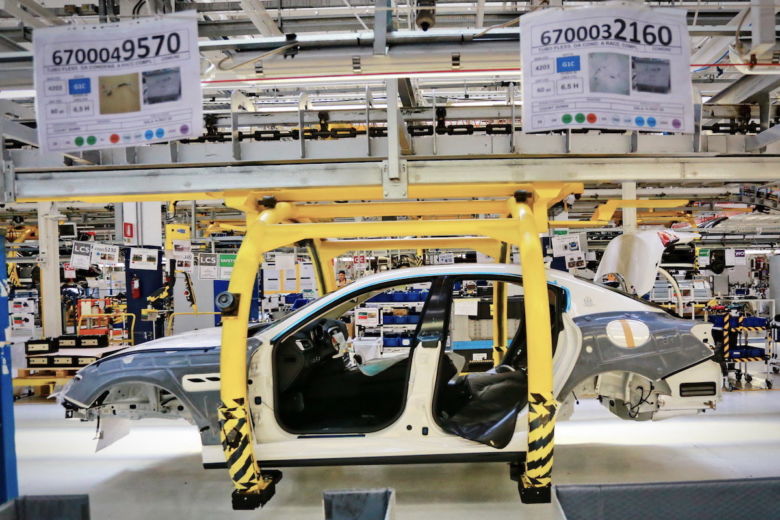
In summary, PU has become a crucial and fundamental part of automotive design, engineering and structural builds. Whilst polyurethane was originally used to aid crash performance and increase durability, its uses have become universal due to an added need for lightweight yet affordable alternatives.
As consumers continue to expect higher degrees of luxury and safety, as well as ongoing increases in fuel cost, the demand for polyurethane is only going to rise. PU’s ability to aid noise reduction, improve safety, reduce weight and assist comfort, will continue to see its use in future vehicle designs.
At Zouch, our specialist automotive and transportation foams are lightweight, flexible and capable of performing to exceptional levels, in even the most demanding conditions. Our in-house design and development engineers are constantly focused on optimum comfort and cost effectiveness, as well as on reducing environmental impact and vehicle weight.
Which is why you’ll find our smart, state-of-the-art products in the interiors, exteriors and engine compartments of thousands of cars, buses, trucks, excavators and recreational vehicles worldwide. Get in touch with our expert team to discuss your specific application and we will support you from prototype to road-ready product.