28th Mar 2018
Optimum Comfort and Performance with Closed Cell Polyethylene Foam in Aircraft Seat Cushioning
In this day and age, it’s important for airlines to make a good and lasting impression with their customers. Just like many other aspects of travel, air transportation is a commodity, but consumers expect a certain level of experience when they embark on a flight to a destination. Whether it’s for business or pleasure, an airline’s customers could be onboard an aircraft carrier for several hours. That means they expect a certain level of customer service as well as comfort.
An uncomfortable ordeal can leave a sour memory of an airline and a passenger is less likely to choose the same airline for their next flight because of it. In recent years, it has grown even more competitive amongst airlines with the added pressure of profitability and their behaviour of overselling flights and cramped seating.
There are easy ways to make commercial flights better experiences for the frequent flyer, through the comfort and performance of onboard seat cushioning. When customers are expected to pay for seat reservations on top of a flight fee - they demand an enjoyable, relaxed, and comfortable space to sit for the duration of their travel.
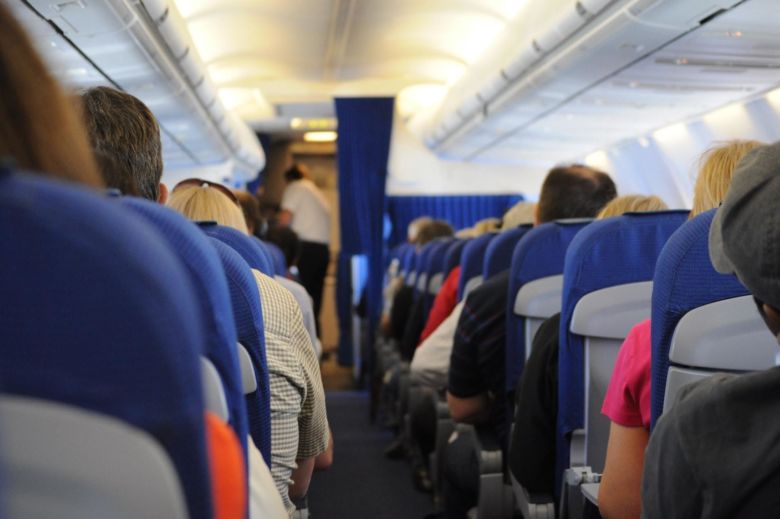
Airlines constantly seek innovation and slimline seating has become part of refurbishing an airlines interior. Airlines benefit from the lightweight and ultra thin seats with lower fuel costs and more space for additional seating. However, for the passengers, slimline seating means discomfort from the thin padding and tight dimension of the seat frames.
Closed cell polyethylene foam allows airlines to reduce weight but maintain the comfort and durability of aircraft seating. Polyethylene foam comes in a wide range of densities and grades, which allows the interior design of an aircraft flexibility to work with a lightweight alternative that is perfect for interior trims, but also provides optimum comfort to the passenger.
Due to the regular use of aircrafts, the seat cushioning is frequently changed and closed cell foam offers a lower cost alternative whilst maintaining the comfort of the passenger. As well as being water resistant, chemical resistant and flame retardant, the increased support of the closed cell composition, allows for significant weight reduction unlike heavier alternatives like urethane foam.
Key benefits of using Closed Cell Polyethylene Foam for Aircraft Seating:
- Absorption of impact and vibration energies
- Support and comfort for the passenger
- Lightweight
- Durable for regular use
- Available in a range of grades and densities
- Water resistant, chemical resistant and flame retardant
- Lower cost alternative
At Zouch, our high-performance closed cell foams, cellular materials and adhesive bonding tapes are trusted by aviation and aerospace specialists right across the world. Designers and engineers choose our advanced materials for aeroplane construction because their low density helps save fuel and, in turn, operating costs as well as providing comfort for passengers.
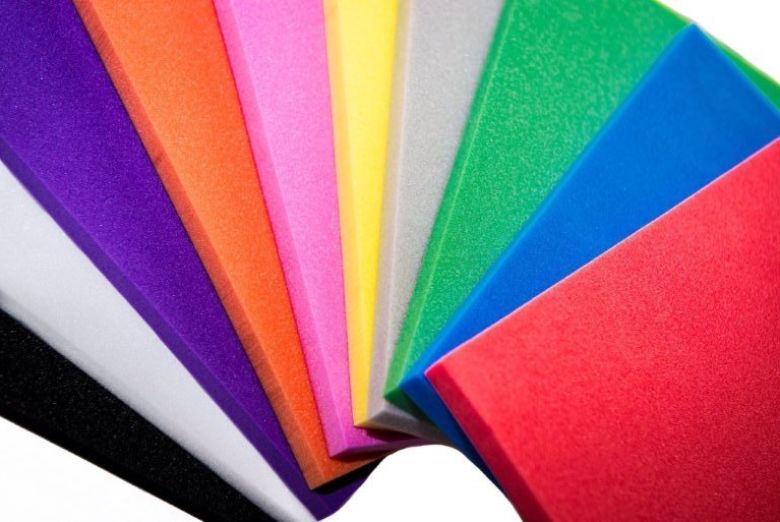
We offer finished foams as vacuum formable or thermo-formable items, CNC routed or die-cut pieces or blank sheets, with or without adhesive backing. However challenging the project, we’ll work with you to source or produce the optimum product for your airline’s interior design. It’s why you’ll find Zouch in cabins and cockpits around the world. Get in touch with you project and speak to one of our experts.